A Comparative Analysis of Powder Coating and Electrophoretic Painting in Industrial Metal Surface Treatment Applications
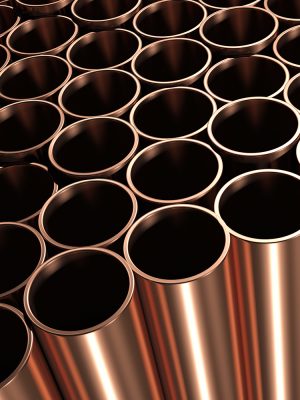
Introduction
In industrial metal surface treatment applications, powder coating and electrophoretic painting are two commonly employed processes. While both methods aim to provide a protective and aesthetically pleasing finish to metal surfaces, they differ in their application techniques, performance, and environmental impact. This article aims to provide a comprehensive analysis of the differences, advantages, and disadvantages of powder coating and electrophoretic painting.
Powder Coating
Powder coating is a dry finishing process that involves the application of electrostatically charged powder particles to a metal surface. The powder adheres to the surface due to electrostatic attraction and is then cured under heat to form a durable and protective coating.
Advantages of Powder Coating:
- Versatility: Powder coating can be applied to a wide range of metal substrates, including steel, aluminum, and stainless steel, and can accommodate various shapes and sizes.
- Durability: Powder coatings are known for their excellent resistance to chipping, scratching, and fading, making them suitable for high-wear applications.
- Environmental Friendliness: Unlike traditional liquid coatings, powder coating does not contain volatile organic compounds (VOCs), making it environmentally friendly and compliant with strict regulations.
Disadvantages of Powder Coating:
- Initial Investment: Setting up a powder coating line requires specialized equipment for powder application and curing, leading to higher initial investment costs.
- Film Thickness Limitations: Achieving consistent and thin film thicknesses can be challenging with powder coating, particularly on complex geometries, leading to potential coating issues.
Electrophoretic Painting (E-Coating)
Electrophoretic painting, also known as E-coating or electrophoretic deposition (EPD), is a process that involves immersing a metal part in a paint bath containing a water-based paint emulsion. An electric field is then applied, causing the paint particles to migrate and deposit onto the metal surface, forming a uniform coating.
Advantages of Electrophoretic Painting:
- Uniform Coverage: E-coating provides excellent coverage and corrosion protection, especially in recessed areas and complex geometries, due to its ability to penetrate hard-to-reach areas.
- Cost-Effective: E-coating is known for its high transfer efficiency, minimizing waste and reducing overall paint consumption.
- Corrosion Resistance: E-coating offers superior corrosion resistance and edge coverage compared to other coating methods, making it suitable for automotive and outdoor applications.
Disadvantages of Electrophoretic Painting:
- Limited Color Options: E-coating typically has limited color options compared to powder coating, which offers a wide range of color choices and finishes.
- Surface Preparation: Extensive surface preparation, including cleaning and phosphating, is essential for achieving optimal adhesion and corrosion resistance in e-coating applications, potentially adding to process complexity and cost.
Conclusion
In conclusion, both powder coating and electrophoretic painting have their unique advantages and disadvantages in industrial metal surface treatment applications. While powder coating offers versatility and environmental friendliness, electrophoretic painting provides uniform coverage and superior corrosion resistance. The choice between these two methods depends on specific application requirements, budget constraints, and desired performance characteristics. As technology and material science continue to advance, innovations in both powder coating and electrophoretic painting are expected to further enhance their capabilities and broaden their applicability in the industrial sector.