Construction and preservation of powder coatings
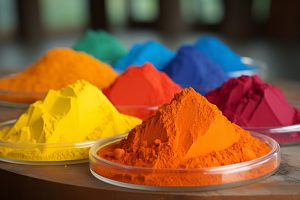
Construction requirements
General powder spraying construction requirements
(1) In order to fully utilize the characteristics of powder coating and extend the service life of the coating film, the surface of the damaged coating must first undergo strict surface pretreatment.
(2) When spraying, the object to be coated must be completely grounded to increase the spraying efficiency of powder coating.
(3) For objects to be coated with large surface defects, conductive putty should be applied to ensure the flatness and smoothness of the coating film.
(4) After spraying, the objects need to be heated and cured. The curing conditions are subject to the technical specifications of the powder products, but the curing temperature and time must be fully guaranteed to avoid quality accidents caused by insufficient curing.
(5) Check immediately after powder spraying. If defects are found, they should be dealt with in time. If defects are found after curing, the scope is small and only localized without affecting the surface decoration of the coated object. The same color powder can be diluted with acetone and repaired. If the scope is large, If it affects the surface quality, polish it with sandpaper and then spray it again or use a paint remover to remove the coating and then spray it again.
(6) The recycled powder must be screened to remove impurities and then mixed with new powder in a certain proportion.
(7) The powder supply barrel, powder spraying room and recovery system should be prevented from being contaminated by other powders of different colors, so they must be purged clean every time when changing colors.
Art-type powder coating construction requirements: Art-type powder has the characteristics of beautiful appearance, strong three-dimensional effect, and good decorative effect, but it has strict requirements on its construction technology
(1) The input air pressure when spraying powder should not be too high. It is generally controlled at 0.5-1.5kg/cm2. Too much air pressure will result in poor pattern clarity or some pitting. The electrostatic voltage should not be too high, generally controlled at around 60-70Kv. If the voltage is too high, the powder attached to the surface of the workpiece will rebound and cause pitting, poor leveling and other defects.
(2) When spraying powder, pay attention to ensure the thickness of the coating film. Generally, control it between 70-100 μm to form obvious patterns and larger patterns. If the coating film is thin, the patterns will not be obvious and the patterns will be small. At the same time, it will Defects such as pitting and bottom exposure appear.
(3) When curing, it must be baked according to the specified temperature and time. If the temperature is too low and the time is too short, the powder will not form patterns, and the mechanical properties will also be greatly reduced due to incomplete curing. In addition, due to the particularity of the art-type pattern powder production process, the pattern will become smaller or less obvious after spraying with recycled powder. Therefore, it is generally recommended not to use recycled powder from art-type powder. It must be tested before use. From the above, although the construction requirements are strict, I believe that as long as the above factors are well grasped during the painting process, ideal and satisfactory results will be achieved.
Storage and handling of powder coatings
(1) Keep away from fire sources and direct sunlight. It should be placed in a well-ventilated place with a temperature below 35°C.
(2) Avoid storage in places easily contaminated by water, organic solvents, oil and other materials.
(3) After using the powder coating, do not expose it to the air at will. The bag should be covered or tightened at any time to avoid the mixing of debris.
(4) Avoid long-term contact with the skin. Powder attached to the skin should be washed clean with soapy water. Do not use solvents.
Safety at coating construction sites
(1) All equipment used in painting operations must be well grounded to eliminate static electricity.
(2) Avoid unwarranted discharge from the coating machine