Application of powder coating additives
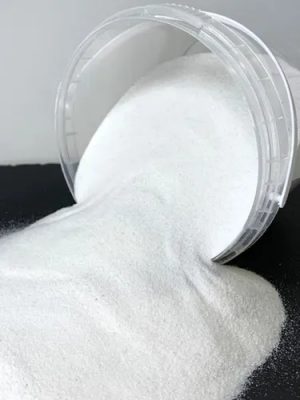
The effects of conventional additives are similar, and the formulas are basically the same. For example, the amount of leveling agent absorbed by epoxy resin is 4% to 5%, and the amount of leveling agent absorbed by silica, called through-flow, is 0.8% to 1.6%. For the dosage of resin and curing agent, first determine the content of the base material in the formula, and then calculate it according to the recommended ratio. Generally, the excess curing agent is 5-10%. So next we will only explain the key products among texture additives and functional additives.
Application of sand texture agent
There are many ways to make sand texture powder. The method of adding more fillers or fumed silica is difficult to extrude and the powder loading rate is not high.
The sand texture agent we use is modified PTTE, which can be added to the powder coating to play a role in physical separation, matting and sanding. The gloss can be reduced to 2 degrees.
Compared with the previous filling method, the extrusion efficiency is high, the wear on the equipment is small, the resin content can be more or less, and the board surface effect is fine and uniform, with good hand feel. When used in conjunction with organic bentonite, the size of the sand particles can be adjusted. If used in the formula Adding an appropriate amount of cellulose acetate can create a silky texture effect.
Sand texture agents are commonly used in the following scenarios:
Interior wall decoration: By applying sand textures of different colors and textures, you can add depth and visual appeal to interior spaces.
Exterior Paint: Using sand texture on exterior architecture can provide additional protection and give the building a unique look. This coating can cover up surface imperfections, such as cracks or dents in walls, and protect against harsh outside weather conditions.
Furniture and Upholstery: Texturing agents can also be used to decorate the surfaces of furniture and other upholstery. By applying a sanding agent to wooden furniture, you can change its appearance and add a natural texture to it.
Application of dotted diffusion agent
Similar to the different patterns of dots made with watercolor pens, the dot diffusion agent drives the pigment to spread when it melts. We call it dot pattern powder. The production of stippling powder requires a two-step method, that is, the stippling agent and the pigment to be diffused are mixed, extruded, and crushed, and the powder in 100-150 mesh is retained, which is called stippling powder.
The base powder used is similar to conventional powder, but without adding flow aids, adding some powder at a ratio of about 1% can make stippling powder. Some powders are added with several different dot powders. This type of powder has a certain degree of contamination and needs to be cleaned slightly after painting.
Application of sponge agent
Cotton agent is mainly used to produce cotton grain (also known as water grain or cloth grain) and reticulated powder. The surface effect of this type of powder is more beautiful and is used by many anti-theft door manufacturers. However, this type of powder has a certain degree of toxicity and can irritate the eyes. Workers are prone to pinkeye after exposure to this type of powder.
In addition, this powder has strict requirements on the thickness of the coating film and baking temperature. Adding a small amount of polyester to the formula can adjust the texture and improve flexibility. Currently, there are three types of sponge agents for epoxy resin, polyester resin, and polyurethane resin.
Application of anti-yellowing agents
The function of the powder anti-yellowing agent is to prevent the polymer from yellowing at high temperatures and prevent the coating film from yellowing when used for too long at room temperature. In addition to the anti-yellowing group, the anti-yellowing agent also has grafting groups that are compatible with the powder resin, which also increases the compatibility and appearance of the coating film. Generally, the adding amount is 1%, and it can keep discoloration for 30 minutes at 220℃.
Application of UV absorbers
UV absorbers are preventive stabilizing additives that can strongly absorb ultraviolet light waves of 270 to 380nm. Their outstanding features are good thermal/light stability and low volatility. They work synergistically with phenolic antioxidants and hindered amine light stabilizers. , protect the polymer from UV damage, thereby improving the weather resistance of the coating film.
Application of powder defoamer
The problem of powder defoaming has attracted more and more attention. When the powder coating is cured, it takes a long time for the air entrained by the workpiece or the coating itself to reach the surface, while the time for the paint to form a film is relatively short, so bubbles or pinholes are formed.
Defoaming agents are mostly used in fine wax powders, and the typical representative is BYK961; the brand with the best domestic application effect is 4430; carbonate treated with ethylene glycol can be used in various powders. Defoaming agent 4430 can not only eliminate pores caused by water in the powder itself, but also eliminate pores in cast iron and aluminum parts caused by plates, improve the fluidity of powder particles and the leveling of powder coatings, and can also replace benzoin to eliminate pores. Yellowing caused by benzoin. However, if the thickness of a single spraying of the powder coating exceeds 200 μm, the disadvantage cannot be eradicated pinholes.
Application of dry powder flow agent
To achieve thin powder coating, the powder particle size must be small. However, the particle size of the powder is relatively fine, and the powder particles are easy to agglomerate, easily clog during spraying, and cause scars after curing. The main function of dry powder flow agent is to reduce the friction between powder particles, thereby reducing the angle of repose, improving the fluidization of the powder during the spraying process, and extending the storage period of the powder.
Application of anti-sticking and hardening series additives
The surface hardness of the coating film has also attracted much attention from powder manufacturers. Products with excellent coating films are often scratched due to friction during packaging and transportation, greatly reducing product quality. The anti-adhesive agent and hardener is an inert polyamide. Such materials can perfectly solve the above problems and have good anti-pollution properties. Some manufacturers also add less than 0.5% anti-adhesive agent when making thermal transfer powder.