Classification of powder coating additives
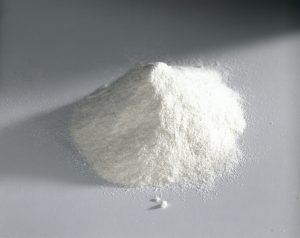
Powder additives are an important component of powder coatings and are necessary substances to improve the performance of powder coatings in certain aspects such as production, construction or coating film. Although the additive amount is much less than that of resin, curing agent and pigments and fillers, and the total amount is generally within 5%, its impact on the performance of powder coatings is extremely important.
An excellent powder coating additive must meet the following conditions: small addition amount and obvious effect, stable physical and chemical properties, no impact on coloring or other properties, easy addition and good dispersion, low toxicity or even non-toxicity, etc. Next, we divide the additives into the following three categories based on their production and application:
Texture additives
Texture additives are powder additives developed to cover the surface roughness of workpieces or achieve beautiful coating effects. It optimizes the previous cumbersome formulas and enables the powder to achieve a more stable artistic decorative effect.
Texture additives can be added in two ways:
Internal addition: Added together with the raw materials when mixing, it can make the recycled powder pattern effect stable and the texture uniform.
Extra: When finished powder is mixed and added, the texture effect is more obvious than that of internal powder, but the texture effect of recycled powder is unstable.
The main varieties include wrinkle agent, hammer texture agent, sand texture agent, sponge agent, foaming agent, moire agent, spot spreading agent, three-dimensional pattern agent, etc. The dosage of texture additives is small, only a few parts per thousand, and is generally extruded and then dispersed. Moreover, these additives have strict requirements on the performance of the resin, such as viscosity, reactivity, glass transition temperature, impurity content, etc.
Ordinary wrinkle powder, if the catalyst content in the resin is high, the lines will be small or no lines will appear. To make cotton grain powder, it is required that the organic chlorine content of the epoxy resin does not exceed 0.1%.
Conventional additives
Conventional additives are necessary additives for the production of ordinary flat powder coatings, mainly including leveling agents, gloss enhancers, benzoin, matting agents, dry powder flow agents, etc. It is used to change the leveling properties of the coating film/the gloss of the coating film/the flow properties of the powder during construction and improve the storage stability of the powder.
Most commonly used leveling agents are polyacrylates, and Tsinghua castor oil, polyvinyl butyral, and cellulose acetyl are also used as auxiliary leveling agents.
Brighteners are coupling agents, dispersants, etc. used to improve the dispersion of pigments and fillers. There are many types of powder matting agents, including chemical types that participate in the reaction and physical types that do not participate in the reaction.
Functional additives
Functional additives are additives that improve and expand the functions of coating films, such as UV protection, anti-aging, impact resistance/adhesion improvement, anti-sticking, flame retardant, antistatic, etc. Functional additives are the fastest growing and most diverse category of additives, such as anti-yellowing agents, ultraviolet absorbers, electrification agents, defoaming agents, light stabilizers, anti-adhesive agents, coupling agents, and adhesion agents. Accelerators, antistatic agents, conductive agents, dispersants, catalysts, heat stabilizers, flame retardants, wear-resistant agents, etc.