Cleaning functions most importantly in maximizing powder coating results
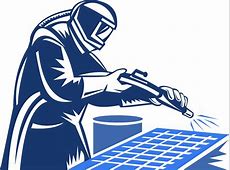
The highest quality powder coating will provide excellent results only if the pretreatment (cleaning, phosphatizing, conversion coating) is done correctly and the overall pretreatment system is maintained up to its potential. Powder coating brings pretreatment back to the basics of cleaning, rinsing, phosphatizing,and seal rinsing.
To maximize the benefit derived from powder, the pretreatment system must provide a clean conversion coated product in a dry state to the powder booth. Surface preparation encompasses more than conditioning or improving a substrate to accept the powder coating. Items that should also be considered include:
- Soils on the substrate;
- Water quality for bath makeup and rinsing;
- Consistent or varying substrates;
- Metals mix-ferrous, nonferrous, yellow metals;
- Metal types-cast, extruded plate, coil, sheet, or combinations;
- Size, weight, dimensions, and configurations of product;
- and System control, maintenance, and record keeping.
Considering all key elements involved in producing a high-quality powder-coated product, one truly stands alone-cleaning. Cleaning is the single most important function in maximizing powder coating results. The degree of cleaning or surface modification is open to a wide interpretation and many differing qualities. For some applications, abrasive cleaning alone is suitable, especially if the final product requires short-to- medium duration adhesion properties.
Leading powder coating and pretreatment manufacturers tend to agree that a high-quality five-stage spray system of cleaning, iron phosphatizing, and final deionized rinsing is the most suitable and preferred method of pretreatment for the widest range of substrates and coating chemistries. Work closely with your pretreatment and powder coating vendor, and select those who work well together on your behalf.
Comments are Closed