Conversion Coating of Galvanized Steel
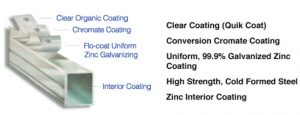
Iron phosphates or cleaner-coater products produce little or non-detectable conversion coatings on zinc surfaces. Many multimetal finishing lines use modified iron phosphates which offer cleaning, and leave micro-chemical etch on zinc substrates to provide adhesion properties.
Many municipalities and states now have limits on zinc PPMs, forcing metal finishers to provide treatment of any solutions in which zinc substrates are processed.
The zinc phosphate conversion coating is, perhaps, the highest quality coating that can be produced on a galvanized surface. To produce a zinc phosphate coating on galvanized, special accelerating agents are required to activate the surface sufficiently to receive the zinc phosphate coating. These coatings are created by the action of bath chemicals on the surface materials. A crystalline zinc phosphate is actually “grown” on the clean substrate surface. In a typical sevenstage zinc phosphating unit, the various stages are:
- Alkaline cleaner.
- Alkaline cleaner.
- Hot water rinse.
- Zinc phosphate processing solution.
- Cold water rinse.
- Post treatment (either chromium or nonchromium type).
- Deionized water rinse.
A six-stage unit would eliminate stage 1, and a five-stage unit would eliminate stages 1 and 7.
In the power spray method of application, the parts to be coated are suspended in a tunnel while the solution is pumped from a holding tank and sprayed under pressure onto the parts. The coating solution is continuously recirculated.
In the immersion method of application, the parts to be coated after being cleaned are simply immersed in a solution of the phosphating solution contained in a stainless steel tank.
The hand-wiping method of application has limited use in conversion coating technology.
Phosphate coatings are usually applied by using five, six, or seven stages. The phosphate
solution is held within a temperature range of 100 to 160°F (38 to 71°C) for spray; 120 to 200°F (49 to 93°C) for immersion; or room temperature for hand-wiping. The applied zinc phosphate coating weight should be 150 to 300 mg./sq. ft.
A processing time of 30 to 60 seconds by spray and 1 to 5 minutes by immersion is usual.
Phosphating solutions have a concentration of 4 to 6% by volume and are applied at spray pressure of 5 to 10 psi.
The zinc phosphate coating is probably one of the best paint base coatings on galvanized steel. A chromium phosphate processing solution does not produce a suitable paint base coating on galvanized steel.
Comments are Closed